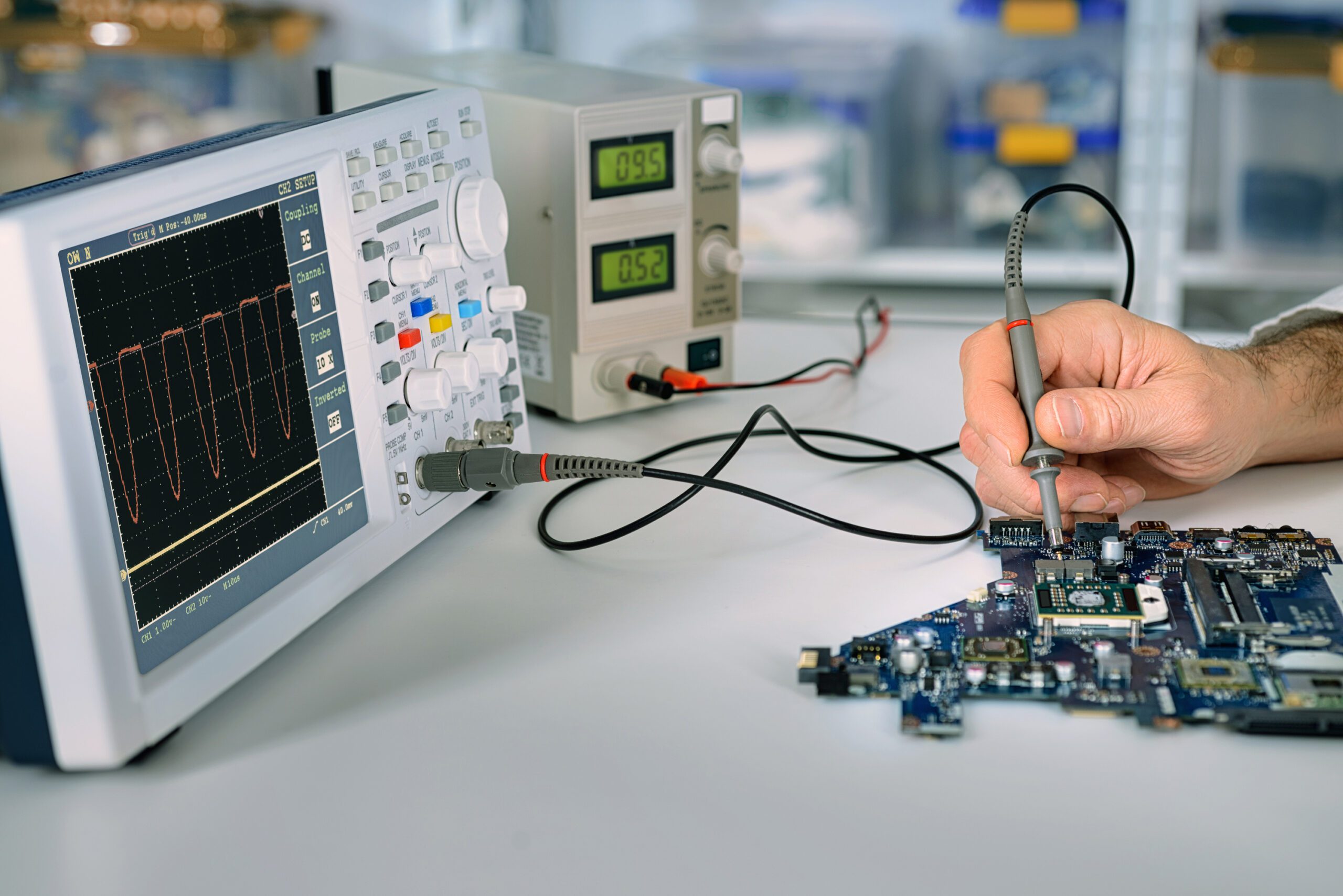
Calibration and Service
Experience Exceptional Support with ATI
At ATI, we are committed to providing exceptional support for all our customers, whether you’re a seasoned user or new to our products. From answering questions to troubleshooting issues, we’re here to help you maximize the value of your investment in ATI equipment.
How Can We Assist You?
- Product Information
Looking for detailed information about a product or accessory? Curious about features, specifications, or compatibility? Use the navigation menu on the left to explore comprehensive product details. For information on discontinued items, visit our Product and Service Availability page, which includes end-of-life (EOL) and end-of-service (EOS) data.
- Product Pricing and Availability
Want to check pricing or lead times? Simply fill out the Contact Us form at the bottom of this page to get the latest updates from our Customer Support team. - Order Support
Need assistance with a recent purchase or tracking a shipment? Our Customer Support team is ready to help. Use the Contact Us form, and we’ll respond within 48 hours with the information you need. - Calibration and Service
Keep your ATI equipment performing at its best with regular calibration and service. ATI provides in-house calibration for all our products, backed by ISO 9001 certification and upcoming ISO 17025 accreditation. Trust ATI for reliable and industry-compliant service. - Technical Support
Experiencing issues with your equipment? Check out our Knowledge Center for quick solutions to common technical challenges. If further assistance is needed, our skilled technicians are here to guide you. - Warranty and Repairs
Questions about your warranty or need to arrange a repair? Visit the Policies page for details on warranty coverage and repair services.
- Documentation
Need an operator’s manual or other documentation? Reach out to our Technical Support team through the Contact Us form, and we’ll ensure you have the resources you need to operate your ATI equipment effectively.
Your success is our priority. Let us know how we can assist you today!
2i Photometer Calibration – ISO 17025 & Aerosol/Electronic Linearity Verification Test (coming soon!)
We ensure that all 2i Photometers meet the highest standards for precision and compliance through our rigorous calibration processes, which include ISO 17025 Certification and the Aerosol/Electronic Linearity Verification Test.
- ISO 17025 Calibration
ATI is the only photometer manufacturer that is ISO 17025 and 9001 accredited. Our 2i Photometers are calibrated in strict adherence to ISO 17025 standards, ensuring that your equipment provides accurate and traceable measurements in accordance with global calibration requirements. ISO 17025 compliance is a critical part of the calibration process to guarantee measurement accuracy for industries that demand the highest level of reliability.
- Aerosol/Electronic Linearity Verification Test
In addition to ISO 17025 certification, all 2i Photometers undergo the Aerosol/Electronic Linearity Verification Test. This test ensures the linearity and responsiveness of your photometer across a wide range of aerosol concentrations, verifying that your equipment can maintain consistent performance in real-world environments. This mandatory process ensures that your photometer operates within strict industry standards, providing dependable data for precise aerosol measurement.
Calibration Services for 2i Photometers
To maintain the optimal performance of your 2i Photometer, regular calibration is essential. Our in-house team of experts ensures that every 2i Photometer is calibrated to meet ISO 17025 standards and passes the Aerosol/Electronic Linearity Verification Test, delivering consistent accuracy and reliability.
- For more information on our calibration services or to schedule a calibration for your 2i Photometer, please contact our Customer Support team using the Contact Us form.
Why Servicing Your Aerosol Generator is Just as Critical as Calibrating Your Photometer
At ATI’s Service and Calibration Laboratory, we’ve consistently seen that customers who service their Laskin and Thermal Aerosol Generators at the recommended intervals experience lower repair costs, fewer performance issues, and greater reliability in their testing systems. Routine servicing ensures your equipment is operating efficiently, safely, and within specification—just like your photometer.
What’s Included in a Thermal Aerosol Generator Service
Our comprehensive servicing process includes:
- Temperature Control: We verify the temperature controller operates within the correct range for optimal aerosol generation. Safety trip points are also tested to ensure safe operation.
- Pressure Regulation Test: We confirm the pressure controller maintains consistent, correct pressure. This prevents damp aerosol or oil droplets from forming, avoiding oil buildup in your test system.
- Leak Testing: We inspect all joints to eliminate oil or inert gas leaks, reducing wastage and improving generator efficiency.
- Electrical Safety Test: We perform a full safety test on all units to meet compliance standards.
What’s Included in a Laskin-Nozzle Generator Service
Our Laskin-Nozzle Generator servicing includes:
- Nozzle Inspection: We check for blockages or debris that could affect particle size and ensure consistent aerosol output.
- Outlet Mesh Cleaning: We remove any buildup that could restrict aerosol flow.
- Oil Reservoir Maintenance: Tanks are drained and thoroughly cleaned to prevent contamination.
- Pressure Gauge Calibration (if applicable): Gauges are removed, calibrated, and verified to ensure accurate pressure readings, which directly impact particle size and output.
- Internal Compressor Check (if applicable): Units with internal compressors undergo a full Electrical Safety Test.
Documentation & Certification
All serviced generators are issued a Certificate of Conformity.
If a pressure gauge is present, a Pressure Gauge Calibration Report is also provided.
Calibration labels are applied to the equipment to clearly indicate service status.
If you require a Particle Size Distribution Certificate, we can arrange that as an additional service.
Comprehensive JSMLT Service – Calibration & Repair at One Price
In addition to our expertise in photometer calibration, we offer comprehensive services for the Joint Services Mask Leakage Tester (JSMLT), a critical device for testing the integrity of respirator masks. Our JSMLT service package includes both calibration and repair at a single, competitive price, ensuring that your equipment remains in optimal condition while minimizing downtime.
- For more details on our JSMLT and Protective Mask Leakage Tester (PMLT) services, including calibration, repair, and training options, please contact our Customer Support team via the Contact Us form, and we’ll respond within 48 hours.
We offer full service and training support for the 100X Automated Filter Tester, a versatile and high-capacity solution designed for testing filter media, replaceable particulate filters, and respirator masks used in both medical and industrial hygiene applications. Our services include operator and service training, ensuring your team is fully equipped to use and maintain the system effectively.
Industry Compliance
The 100X Automated Filter Tester is designed to meet rigorous global industry standards, including:
|
![]() |
Applications
|
|
The 100X is specifically engineered to test N95, KN95, FFP, and P100 respirator masks, making it an ideal solution for both development and production quality control environments.
For further details on service, training, and how the 100X can meet your testing needs, please reach out to our Customer Support team.
Additional Services to Support Your Compliance and Operational Excellence
In addition to our core calibration and service offerings, ATI provides a range of miscellaneous support services designed to streamline your documentation, compliance, and operational readiness.
- Certificate of Origin
We can provide a Certificate of Origin for your equipment upon request—essential for international shipments, audits, and traceability documentation. - Custom Test Reports
Whether you need tailored data formats or client-specific templates, we can generate test reports customized to meet your internal or regulatory requirements. - Particle Size Distribution Certification
Available upon request for aerosol generators, this certification provides detailed insight into particle characteristics for validation and regulatory submission purposes.
Training Designed for Real-World Application
The ATI Training Institute offers a comprehensive range of training options tailored to your team’s needs—available virtually, on-demand, or on-site. We specialize in deep technical training on:
- Photometer usage and maintenance
- Understanding and applying industry standards
- Cleanroom and containment facility testing procedures
Whether you’re upskilling a new team or preparing for compliance audits, our training ensures your staff is confident and capable.
![]() |
![]() |
![]() |